Content
Project management as mission possible
Project management – a buzzword that many like to write on their banners. In an extensive development process, Goerner has been engaged with the support of projects, and has made their management into their "mission possible". In this way, we guarantee our partners and customers a significant increase in efficiency, measurable time, resource and cost quality on top of individual solutions.
Our company is set up in such a way that allows us to adapt to the planning and production requirements of the market and customers quickly and in an uncomplicated manner.
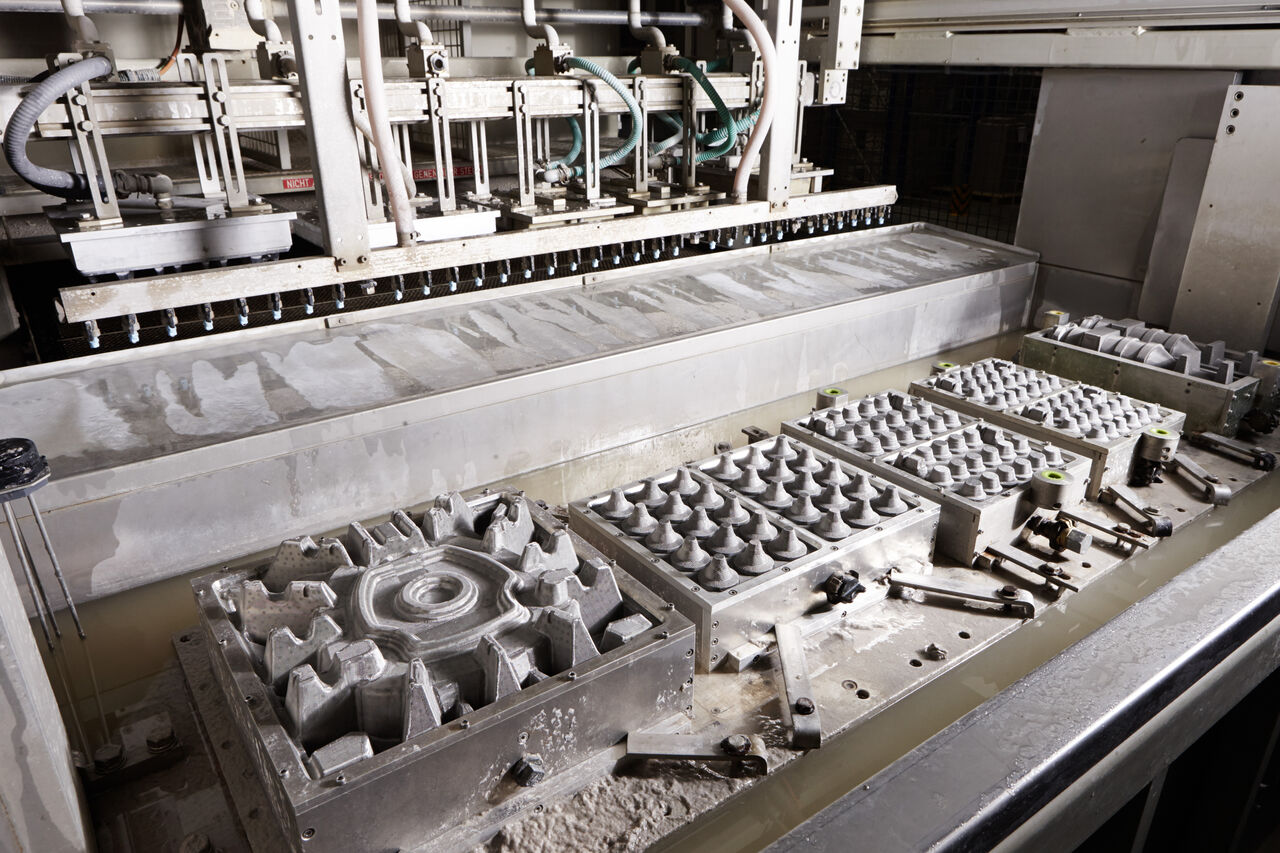
Perfect results due to the the most modern CAD technology and extensive know-how.
Our guides are the requirements of the customer.
Optimum solutions individually implemented guarantee our customers cost advantages and packaging efficiency: Precision fit, stability, speed of handling. You have a request – we deliver proposals and innovative ideas. Solution competence is at the heart of all we do:
Personal support from the design definition up to delivery
Individual design development
Visualisation and model construction
Development up to series production
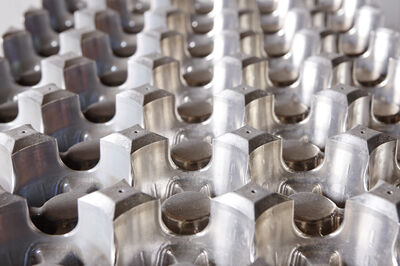
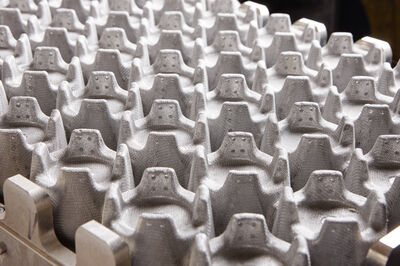
Tool making
Whoever works with standards hardly ever achieves exclusivity.
Standard tools are mostly the wrong companions for achieving individual solutions. Our company develops and builds the required tools on site based on the most modern CAD technology. The joint goal of our trained and experienced team is always to have protective packaging with the exact dimensions and the highest quality level in their hands at the end of a successful day.
Production
We know what our goal is. We know what we need to achieve this. We simply know what we are doing here.
Fibre preparation
Paper and cardboard waste are dissolved in a pulper and then pumped into a thick stock chest. Finally, the thick stock is diluted to approx. 6 percent via a control system and transferred into the work vat.
Wooden frame
The vertically working wood frame, together with the tools, is dipped into the work vat with the mixture of substances. The tool suctions the mixture of substances through the sieves by means of vacuum. Fibres are retained by the sieves, thus building up the mould. After being lifted out, the moulded parts are removed from the sieve by means of a counter-mould and vacuum and are placed on the drying section.
Drying path
The drying path consists of a latticed transport belt which enables ventilation. Drying hoods blow heated air created by liquid gas onto the moulded parts The final humidity of the moulded parts is approx. 5 percent. At the end, the moulded parts are removed and placed on pallets
Mould press and die
Je nach Kundenwunsch können die Formteile nachgepresst werden. In einer Presse werden unter Hitzeeinwirkung die Formteile in ihrer Passgenauigkeit stabilisiert und fixiert. Zusätzlich können gewünschte Prägungen und Perforierungen eingearbeitet werden.
Finishing
Special colourations and surface structures are no problem due to flocking. This creates velvety surfaces, e.g. through viscose or polyamide fibres.
Download
- Ablaufbeschreibung Formpack (DE)653 KBDownload